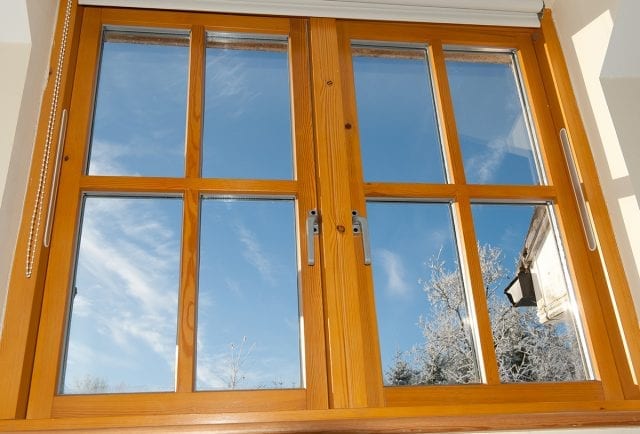
The wood is an eternal material. In construction, it has been used since the first structures that men have built. With the later development of glass and its capabilities – wooden windows become a required element of the building processes. In recent decades, they have lost their primacy due to the development of PVC materials.
However, as a natural, healthy and comfortable material, they are now returning to the “scene” again.
Wood As Material
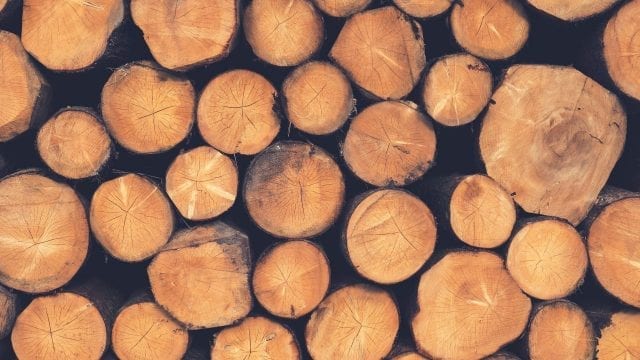
Wood is an irreplaceable material because of its good physical, mechanical and technical properties. As a natural material, wood “breathes” and has excellent thermal and sound insulation, and unlike all other materials, it can diffuse steam. Timber windows can disperse excess moisture from the outside by diffusion, as well as to inject the necessary moisture into the room.
Thus, when during the winter the air inside the house is excessively dry due to heating – the wooden windows leak wood moisture from the outside and diffuse it into the room.
The so-called healthy climate exchange is due to wood pulp and hence the expression that “wood breathes”.
Pros And Cons Of Timber Windows
Each material has its advantages and disadvantages. Due to the favourable price/performance ratio, in recent years PVC materials have taken over in the selection of joinery materials. Nevertheless, wood as a natural material has many positive characteristics.
One of its disadvantages is its slightly more demanding maintenance, but thanks to modern technology, there is more and more progress in this field. Improved mechanical and physical properties of the wood and greater stability of the wood are achieved by its treatment. That implies lamination, glueing of wooden elements, then heat treatment – drying of water content, etc. Proper woodworking and construction maximize profile stability and dramatically improve the performance of a wooden window.
Thermal Insulation
As for thermal insulation, which is one of the first features to consider when it comes to exterior joinery – the thermal resistance of the window frame increases with its thickness. According to the European regulations on thermal energy saving, the passage of heat through the window should not exceed 1.6W / m² for windows with wooden profiles.
The total heat transfer through the window is determined by the average heat transfer of the frame and the glass, taking into account the heat losses in the joints.
Eco-Advantages
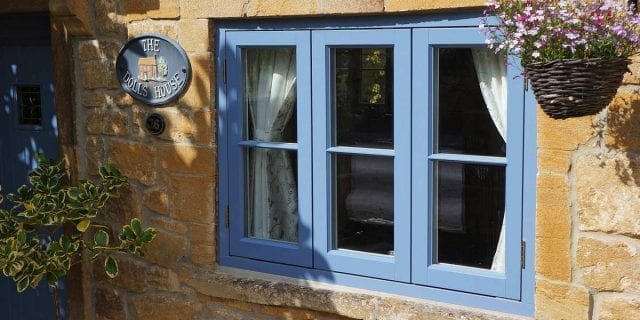
For timber windows, coniferous wood is mostly used in window frames. Wood as a characteristic material has precedence over PVC mostly because of its environmental factor. It is a common combination of timber on the inside of the window frame, while the outside is made out of aluminium.
Window outlines combined like that – utilize the precedences of both materials. Wood is a common material that has great warm protection, dimensional solidness and high endurance. On the other hand, aluminium furnishes the wood with UV protection, heat and frost. The air between the aluminium and wooden profiles additionally permits great ventilation.
Which Type of Wooden Windows to Choose?
Wood is a bright, strong, and attractive material. It is a good insulator, reasonably priced, and can always be found in an unlimited range of shapes and profiles. Plus, with a little regular care, it will last you a lifetime. The biggest problem is finding the right kind of wood that will best suit your home style.
That’s enough to make your headache. Most often they are made of sweet chestnut or teak, but also of laminated solid wood, oak, beech, cherry, linden, etc. When using the materials, not only the installation process and the life of the windows must be kept in mind – but the manufacturing process as well. Among all building elements, wooden elements require the least energy to prepare and process.
Manufacture Of Timber Windows
https://www.youtube.com/watch?v=ZzJcLAKWVzA
We will try to show you some of the stages of window manufacturing and bring you closer to the experience of some well-known manufacturers such as Dempsey Dyer Ltd. Laminated timber is used as the starting material. It is irreplaceable for many reasons, and above all because of its mechanical and aesthetic properties. The quality and price of the slats depending on the quality and the type of timber being laminated.
1. Special Preparation
At this stage, it ranges from the dimensions of the openings (construction measures) in which the joinery is placed. Special, or technical preparation, refer to the choice and type of slats from which the windows are made. This phase also covers activities such as cutting list, specification of auxiliary materials, etc.
2. Cutting The Elements
After selecting the slats, the first stage of production is to cut them according to the prepared cutting list. The longer elements are first produced and the rest of the slats are used for the shorter ones.
3. Stabilization
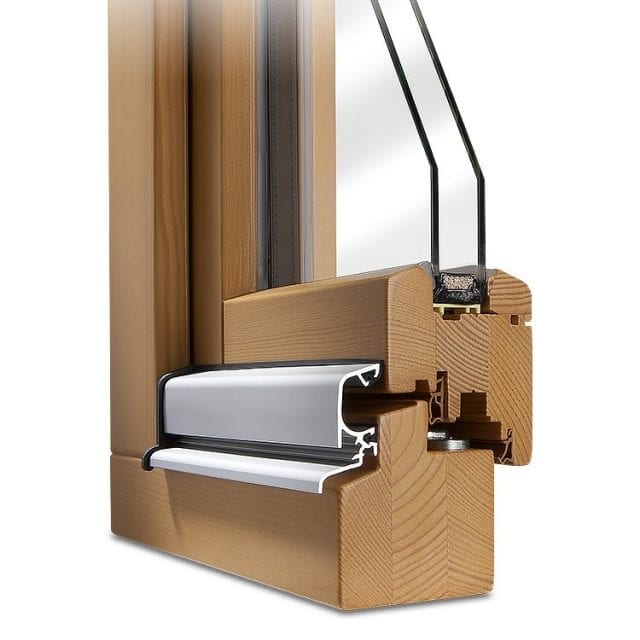
This is a phase that many manufacturers avoid. Specifically, slats can look straight and without deformations. After cutting into the elements, internal stresses can occur. This can have a significant effect on the straightness and proper dimensions of the elements. Therefore, the cut elements are left to stand for at least one week
4. Pre-Woodwork Analysis
After the stabilization phase, an experienced carpenter carefully analyzes each element and decides which side to straighten, to eliminate any possible geometric errors. The operation is performed on a standard woodworking plane. This operation neutralizes the stresses and stabilizes the structure of wood, providing the maximum use of each element.
5. Planing Timber Slats
Upon completion of the pre-woodworking operation, the elements are forwarded to a four-sided planer where all four sides are machined in one pass. In doing so, a final cross-section of the element is achieved, which enables it to move to the next processing stage.
6. Bonding
The next operation involves the glueing of the finished elements, that is, the formation of frames. This operation is performed in a special press. Thanks to hydraulic pistons, frames of exact dimensions and shapes are formed. After the glueing operation, the joints exhibit excess adhesive as a result of the pressure and the plug-to-plug connection. The adhesive is removed manually and easily, provided that it is carried out immediately after the joining operation – ie the formation of the frames.
7. Profiling
The formed sash windows remain dry for at least two days after cleaning. Afterwards, they can go into further processing. This phase provides the exterior profiling with quality and sharp tools, to provide profiles that allow perfect fitting to the frame. The sash is machined on all four sides.
8. Grinding
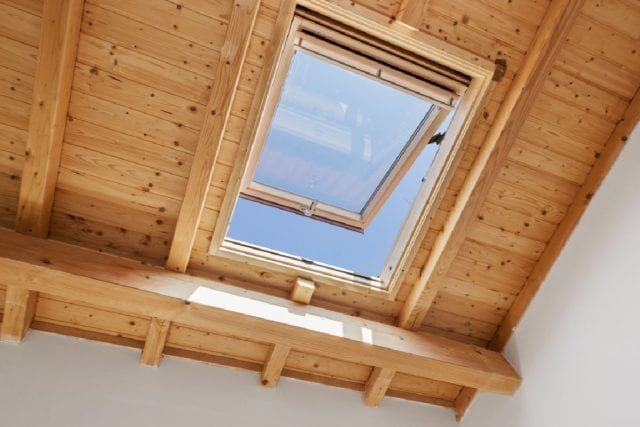
After drying, the surfaces are followed by grinding which is carried out on a wide-angle flow grinder made up of three working rollers. The rollers are of different granularities, and the grinding is done in one pass.
The finest roll is used to sand varnished surfaces. Grinding is performed with a special grinder. The machine can be one-sided or double-sided, as well as with multiple operating functions.
9. Drill For Handle
After grinding, the window sash is drilled on a special machine of high accuracy. This operation is performed with a work unit that achieves triple drilling in one stroke. In this way, the super-accurate positioning of the closing lever is achieved relative to the locking mechanism.
10. Final Control
This phase eliminates any grinding defects and verifies all elements that should be contained on the window before painting.
Of course, these are not all stages in timber window fabrication. All this is followed by painting, impregnation, brushing, finishing lacquer, installing gaskets and bumpers, mounting shutters, etc. In the end, we get the final product ready for delivery.
Conclusion
When you decide to replace your old wooden windows, be aware that they will not look like your old ones. The quality of today’s younger lumber is not comparable to old. If new windows represent an ever better future, then they are certainly one good story you don’t want to miss!