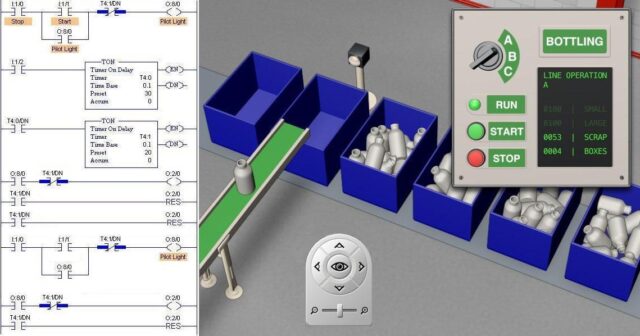
Programmable logic controllers (PLCs) are the backbone of many industrial automation systems. With their ability to automate complex processes quickly and accurately, these digital devices have revolutionized manufacturing operations around the world.
PLCs can be used to control a wide variety of machines, from medical equipment to large-scale production lines. They offer numerous benefits for any company looking to streamline its operations and increase efficiency.
This article covers the various uses of PLCs, their associated advantages as well as training considerations when using them in industrial applications. We will also look at some common challenges that may arise due to improper implementation or lack of knowledge about programming them correctly.
By understanding how PLCs work and what they can do for your business, youll be able to make informed decisions on whether or not this technology is right for you.
Benefits of PLCs:
PLCs offer many advantages to industrial and commercial businesses. By using a PLC, businesses can automate processes or operations more quickly and easily than with manual control systems. This automation helps reduce labor costs, improve safety conditions, provide better process control accuracy, increase efficiency in production lines and decrease downtime due to equipment malfunctions.
Additionally, using a PLC allows for remote monitoring of machines which can be used for predictive maintenance or identifying problems before they become too costly. Furthermore, when compared to traditional hardwired logic controllers that require extensive wiring between devices and the controller itself; PLCs are much easier to install and maintain due to their flexibility in terms of programming capabilities as well as communication protocols with other connected devices via its I/O ports.
All these aspects make Programmable Logic Controllers an ideal choice for any business looking into automating their processes.
Improved Reliability and Performance
PLCs are renowned for their improved reliability and performance. With built-in features such as predictive maintenance, self-diagnostics, and fault monitoring, PLCs provide a reliable solution that can reduce downtime costs associated with unanticipated maintenance or repair.
Additionally, the ability to quickly adjust settings on the fly makes them ideal for optimizing system performance in real time. This scalability allows users to tailor each PLC’s function to meet specific needs while maintaining operational efficiency and accuracy.
Furthermore, due to their durability and modular design they can withstand harsh environmental conditions without losing any of its capabilities. All of these benefits make it easy to understand why so many businesses rely on PLCs when it comes to controlling processes in different industries.
Reduced Maintenance Costs
The use of Programmable Logic Controllers (PLCs) in industrial processes can lead to significant cost savings through reduced maintenance costs. PLCs are designed to be reliable and robust, meaning that they can withstand harsh environments while still maintaining their performance.
This durability means that fewer repairs and replacements are needed over time, making them a great long-term investment for any business. Additionally, PLCs allow for remote monitoring of systems which reduces the need for expensive onsite inspections.
With built-in diagnostics features, potential problems can be identified quickly allowing corrective actions to be taken before they become major issues. As a result, businesses will experience lower overall maintenance costs with the use of Programmable Logic Controllers (PLC).
Uses of PLCs:

PLCs can be used to control a wide range of industrial processes, from manufacturing and packaging lines to automotive applications. PLCs are designed for reliability and flexibility in order to ensure that production runs smoothly and efficiently.
Additionally, they have considerable memory capacity so that changes can be made quickly without disrupting the systems functionality or performance. In terms of safety, PLC systems are equipped with sensors that can detect potential hazards before they cause damage or harm.
Finally, PLCs often come with software packages which allow users to easily program the system according to their needs without requiring an extensive amount of technical knowledge.
-Industrial Automation Process Control Applications
Industrial automation process control applications are the key to a successful manufacturing operation. Programmable logic controllers (PLCs) are an integral part of this system, allowing for greater accuracy and increased production efficiency.
PLCs are used to monitor and control industrial processes, providing real-time data on temperatures, pressures, flow rates, speeds, angles and more. They can be programmed to respond automatically in emergency situations or when certain conditions are met such as low stock levels or excessive heat build up.
With advances in technology, PLCs offer numerous benefits that make them invaluable tools for any industry looking to increase productivity while decreasing costs. Training is essential for operators who wish to use PLCs effectively; this training covers basic theory and practical application of the equipment so they can get the most out of their machines with minimal downtime due to errors or malfunctions. Additionally it is important that engineers understand how best to design systems using modern techniques such as ladder logic programming which allows complex actions with only a few lines of code.
The right combination of hardware components and software implementation ensure smooth running operations with minimum effort from personnel involved in managing these automated systems leading ultimately towards improved profit margins for businesses across multiple industries worldwide
-Building Automation Systems
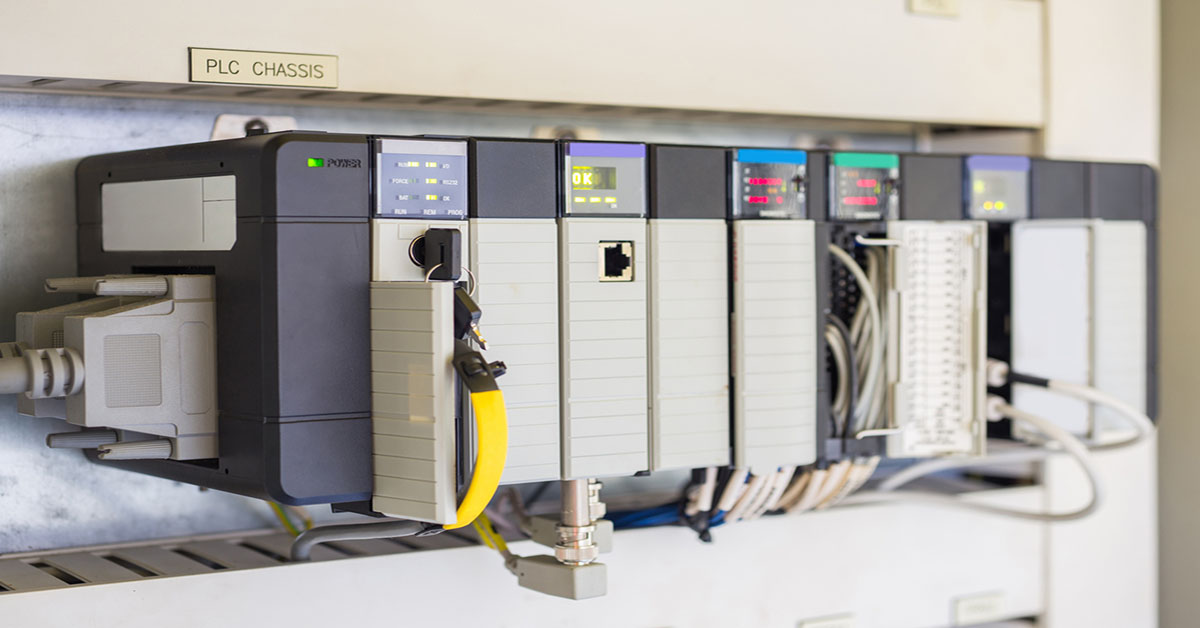
Building Automation Systems (BAS) are increasingly becoming more popular as a way to increase efficiency and safety in industrial settings. These systems can be used to monitor and control the environmental conditions of a facility, such as temperature, humidity, chemical concentrations, air quality or security.
The devices that make up these systems include programmable logic controllers (PLCs), which allow users to customize their BAS with specific tasks for each device. PLCs offer many benefits over traditional automation solutions; they are reliable, cost-effective and require minimal maintenance.
Additionally, PLCs provide an easy to use interface that makes training personnel straightforward. With proper instruction on how to operate the system and troubleshoot any issues that may arise during its operation, personnel will be able to keep operations running smoothly even when changes occur in the environment or equipment used by the system.
Conclusion
Programmable Logic Controllers (PLCs) offer a cost-efficient and reliable solution for industrial automation, making them a popular choice among factories and production facilities. Their ease of programming and powerful features make them suitable for many different applications.
Through proper training, individuals can gain the skills necessary to use PLCs effectively in any system, allowing businesses to get the most out of their automation investments. With its versatility and reliability, its no wonder why Programmable Logic Controllers are so widely used across various industries today.