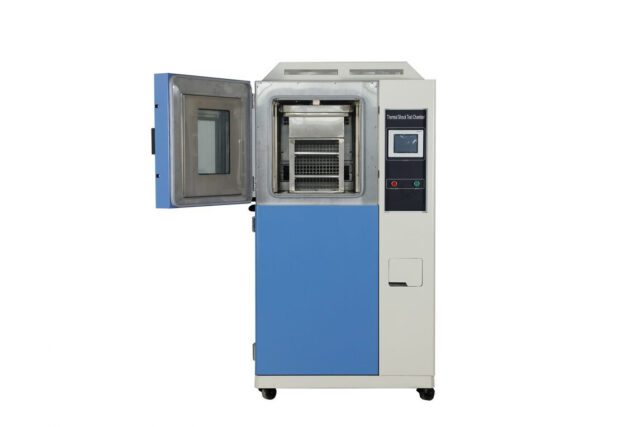
The durability of products and materials is essential to the success of any industry. As technology continues to evolve, so do the challenges facing these industries when it comes to ensuring their products can withstand extreme temperatures and environments without being damaged or destroyed in the process.
To help evaluate this durability, two-zone thermal shock chambers have been developed as a way for companies and researchers to measure how well their materials can handle high-stress conditions. In this article, we will explore what two-zone thermal shock chambers are and why they have become such an important tool in material testing today.
Durability Testing with Thermal Shock Chambers

When it comes to evaluating the durability of products, two-zone thermal shock chambers are a reliable and efficient tool. These chambers work by exposing parts or components to extreme temperature swings to test their reaction.
This testing process can help engineers identify weaknesses or potential failure points before they become an issue in the real world. By utilizing these thermal shock chambers, manufacturers can ensure that their products will stand up to even the most demanding environments and conditions.
The two-zone thermal shock chamber is designed for rapid cycling between hot and cold temperatures with minimal downtime for setup and loading/unloading from each zone. It also features precise temperature control so that temperatures remain consistent throughout testing cycles, providing accurate results every time.
Evaluating Product Performance in Extreme Conditions
When it comes to evaluating the performance of products in extreme conditions, two-zone thermal shock chambers provide an invaluable resource. With a wide range of temperatures and rapid transitions between them, these chambers can accurately simulate environments that would be too hazardous or difficult for human testing. By exposing materials to oscillating temperatures within the chamber, manufacturers can determine how durable their products will be under real-world application scenarios.
This type of testing gives engineers valuable insight into product design decisions and allows them to ensure consumer safety while pushing the boundaries of innovation. As technology advances, so does our ability to evaluate products in increasingly hostile conditions; two-zone thermal shock chambers continue to remain at the forefront with reliable results every time.
Understanding the Benefits of Two-Zone Thermal Shock Chambers

When it comes to testing products for durability, two-zone thermal shock chambers are essential. This type of testing replicates the extreme temperature changes a product may experience in its lifetime and can identify potential weak points that need to be addressed before the product is released for sale.
Understanding how two-zone thermal shock chambers work and what kind of benefits they provide is important for any company looking to produce reliable products. One advantage of using two-zone thermal shock chambers is their ability to replicate rapid temperature changes that would normally take days or weeks in a natural environment.
This means that manufacturers can quickly evaluate how well their products stand up against such conditions without lengthy waiting periods or expensive field tests. Additionally, these types of tests allow companies to get results quicker than ever before, giving them more time to make appropriate changes if needed.
Another benefit offered by two-zone thermal shock chambers is the insight into material failure mechanisms they provide. By studying which parts fail under certain temperatures and pressure levels, engineers can learn where improvements need to be made or which materials should be used instead in order further increase reliability over time.
Conclusion
In conclusion, Thermal Shock Chambers are an effective way to evaluate the durability of a product or material when exposed to extreme temperature changes. By testing components in such chambers, engineers can make informed decisions on their design choices and determine if they will be able to withstand challenging environmental conditions.
Ultimately, this helps manufacturers produce reliable products that stand up against even the most severe temperature fluctuations.